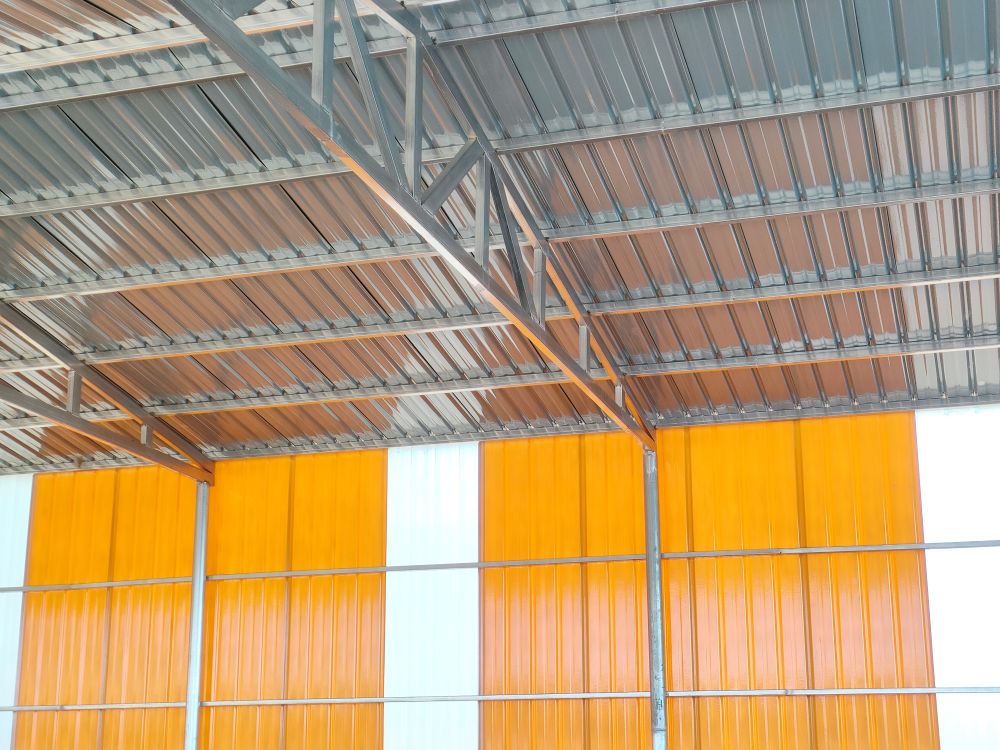
Meta Description: FRP sheets for mining: Cut downtime & maintenance costs by 60% with corrosion-proof walkways, ducting, and structures. Engineered for extreme environments. Get a quote!
FRP Sheets: The Mining Industry’s Answer to Corrosion, Safety, and Cost Efficiency
The mining industry faces relentless challenges: corrosive chemicals, heavy impacts, and harsh environments that degrade traditional materials. FRP (Fiber Reinforced Plastic) sheets are transforming mines worldwide by delivering unmatched durability, safety, and ROI. As a leading FRP manufacturer, we engineer solutions that outlast steel, concrete, and wood in the planet’s toughest conditions.
⚙️ Critical Mining Applications for FRP Sheets
Corrosion-Proof Walkways & Platforms
Resist acids, alkalis, and salt spray in processing plants.
Non-slip surfaces reduce worker falls in wet/slurry areas.
Ventilation & Exhaust Ducting
Immune to sulfuric acid and chemical fumes in smelting zones.
70% lighter than steel for faster installation in confined shafts.
Safety Structures & Guarding
Non-conductive panels for electrical safety near substations.
Impact-resistant machine guards that won’t crack or corrode.
Material Handling Solutions
Lining for chutes, hoppers, and slurry trenches with near-zero friction.
UV-stable roofing for outdoor stockpiles and equipment shelters.
💥 Why Mines Choose FRP Over Traditional Materials
Challenge | Steel/Concrete | FRP Sheets |
---|---|---|
Corrosion | Rusts, spalls, fails in 2–5 yrs | 25+ year lifespan; inert to chemicals |
Maintenance | High-cost welding/repainting | Near-zero upkeep; no coatings needed |
Weight | Heavy (requires cranes) | 70% lighter; manual handling possible |
Electrical Risk | Conductive | Non-conductive (ideal for HV areas) |
Total Cost | 3–5x lifetime expenses | ROI in <3 years via reduced downtime |
✅ Engineering Advantages Mine Operators Trust
Extreme Durability: Withstands pH 1–14, temperatures from -40°C to +120°C.
Fire Safety: UL 94 V-0 rated & ISO 4589-2 compliant (low smoke toxicity).
Custom Fabrication: Sheets cut to size with anti-static or fire-retardant additives.
Easy Retrofit: Bolt-on installation minimizes operational disruptions.
📊 Case Study: Copper Mine in Chile
Replaced steel walkways with FRP sheets in leaching tanks area. Result: Maintenance costs dropped 62%, and zero structural failures in 4 years despite constant acid exposure.
💡 The Economic Impact: Less Downtime, More Profit
Mines lose $10,000–$50,000 per hour during unplanned shutdowns. FRP eliminates:
Production halts for corrosion repairs.
Scaffolding costs for high-access maintenance.
Premature asset replacement (conveyor covers, grating, etc.).
✨ Why Partner With Us?
As FRP manufacturers with 20+ years in industrial solutions, we offer:
Mining-Specific Engineering: Load-optimized thickness (3mm–30mm) and rib designs.
Global Certifications: ISO 9001
End-to-End Support: From CAD drawings to on-site installation guidance.
Rapid Delivery: Standard sizes shipped in 48 hrs; custom orders in 2 weeks.
Conclusion: In mining, every minute and dollar counts. FRP sheets aren’t just a material upgrade—they’re a strategic investment to slash costs, boost safety, and conquer corrosion for decades.