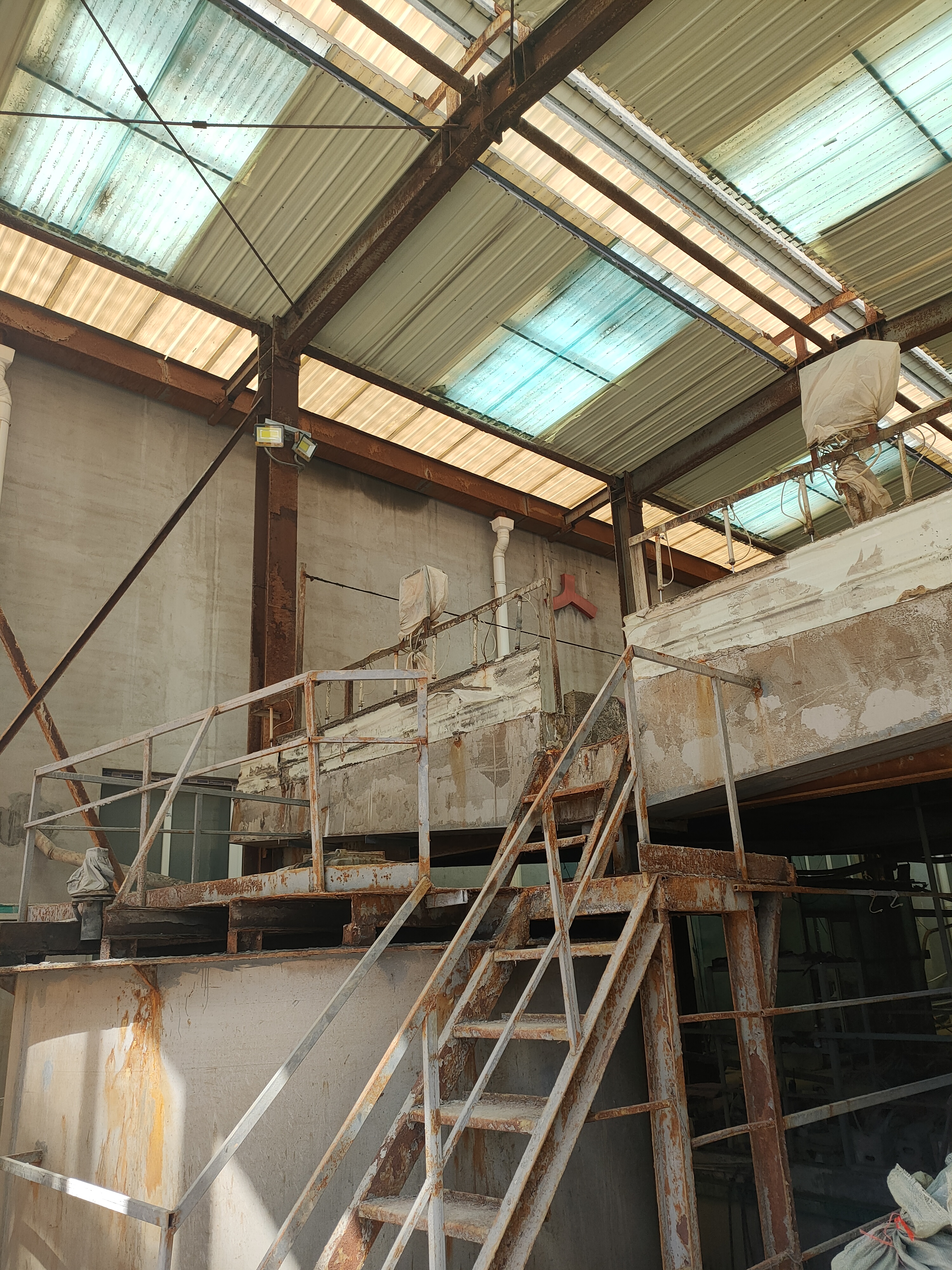
Corrosion is a silent destroyer, costing industries billions annually in repairs, replacements, and operational downtime. Traditional materials like steel, aluminum, and wood often succumb to rust, chemical degradation, and environmental wear. Enter FRP (Fiber-Reinforced Plastic) sheets—a lightweight, durable, and non-corrosive alternative revolutionizing industries from marine engineering to chemical processing. In this guide, we’ll explore how FRP solves corrosion challenges, its advantages over conventional materials, and best practices for implementation.
1. The Problem with Corrosion: Causes and Consequences
Corrosion occurs when materials react with their environment, leading to structural weakening. Common types include:
Galvanic Corrosion: When dissimilar metals interact in conductive environments (e.g., saltwater).
Chemical Corrosion: Exposure to acids, alkalis, or solvents.
Pitting and Crevice Corrosion: Localized damage from stagnant moisture or chlorides.
Industries at Risk:
Marine: Saltwater rapidly degrades metal hulls, docks, and offshore structures.
Chemical Processing: Tanks and pipes face constant exposure to corrosive substances.
Wastewater Treatment: Chlorine, sulfides, and humidity accelerate material breakdown.
The Cost of Ignoring Corrosion:
Safety hazards from structural failures.
Frequent maintenance and replacement expenses.
Operational downtime impacting productivity.
2. How FRP Sheets Defy Corrosion
FRP combines fiberglass reinforcement with polymer resins (polyester, vinyl ester, or epoxy) to create a material inherently resistant to corrosion. Here’s why it works:
Material Advantages:
Non-Reactive Polymers: Resins like vinyl ester withstand acids, alkalis, and solvents.
No Galvanic Corrosion: FRP doesn’t conduct electricity, eliminating reactions with metals.
Protective Gel Coat: A factory-applied layer shields against UV rays, chemicals, and abrasion.
Key Benefits:
Zero Rust or Rot: Unlike steel or wood, FRP won’t rust, warp, or decay.
Longevity: Lasts 20+ years in harsh environments vs. 5–10 years for steel.
Low Maintenance: No need for coatings, paints, or frequent inspections.
3. Industry-Specific Applications of Corrosion-Resistant FRP
Marine and Offshore
Boat Hulls and Decks: Resists saltwater, fuel, and bilge chemicals.
Docks and Pilings: Withstands tidal forces and marine organisms.
Case Study: A coastal shipyard reduced hull repair costs by 60% after switching to FRP panels.
Chemical and Petrochemical Plants
Storage Tanks: Handles sulfuric acid, caustic soda, and hydrocarbons.
Ventilation Ducts: Immune to fume-induced degradation.
Wastewater Treatment
Grating and Walkways: Survives chlorine, hydrogen sulfide, and constant moisture.
Cover Panels: Protects equipment in humid, acidic environments.
Oil & Gas
Pipe Supports and Platforms: Resists oil, gas, and saline exposure.
4. Customizing FRP for Extreme Environments
Not all FRP is created equal. Tailor your sheets to specific challenges:
Resin Selection
Vinyl Ester: Best for acids, high temps (e.g., chemical tanks).
Epoxy: Superior adhesion and chemical resistance for pipes.
Polyester: Cost-effective for general-purpose use.
Additives and Enhancements
UV Inhibitors: Prevent sun damage in outdoor installations.
Fire Retardants: Meet safety standards for industrial settings.
Antimicrobial Coatings: Ideal for food processing or wastewater facilities.
Design Tips
Optimize thickness for load-bearing needs.
Use smooth finishes to prevent debris buildup.
Avoid metal fasteners to prevent galvanic reactions.
5. Installation and Maintenance Best Practices
Installation Guidelines
Prepare the Surface: Ensure it’s clean, dry, and free of contaminants.
Use Non-Metallic Fasteners: Fiberglass or composite bolts prevent galvanic corrosion.
Seal Joints: Apply waterproof sealant to block moisture ingress.
Maintenance Tips
Clean surfaces with mild soap and water—no harsh chemicals needed.
Inspect annually for scratches or gel coat damage (easily repairable).
Avoid abrasive tools that could compromise the protective layer.
6. FAQs About FRP and Corrosion
Q: Can FRP corrode?
A: FRP doesn’t rust or corrode like metals. However, improper resin selection or physical damage (e.g., deep scratches) can reduce effectiveness.
Q: Is FRP more expensive than steel?
A: Initial costs are higher, but FRP saves 30–50% long-term by eliminating maintenance and replacements.
Q: How does FRP handle high temperatures?
A: Specialty resins (e.g., vinyl ester) withstand temps up to 300°F (150°C).
Q: Can FRP be recycled?
A: Yes! Many FRP products are recyclable, aligning with sustainability goals.
Conclusion
Corrosion doesn’t have to be a costly headache. FRP sheets offer a scientifically proven, durable alternative to traditional materials, slashing maintenance costs and extending infrastructure lifespans. By partnering with an experienced FRP manufacturer, industries can design corrosion-resistant solutions tailored to their unique challenges—ensuring decades of reliable performance.