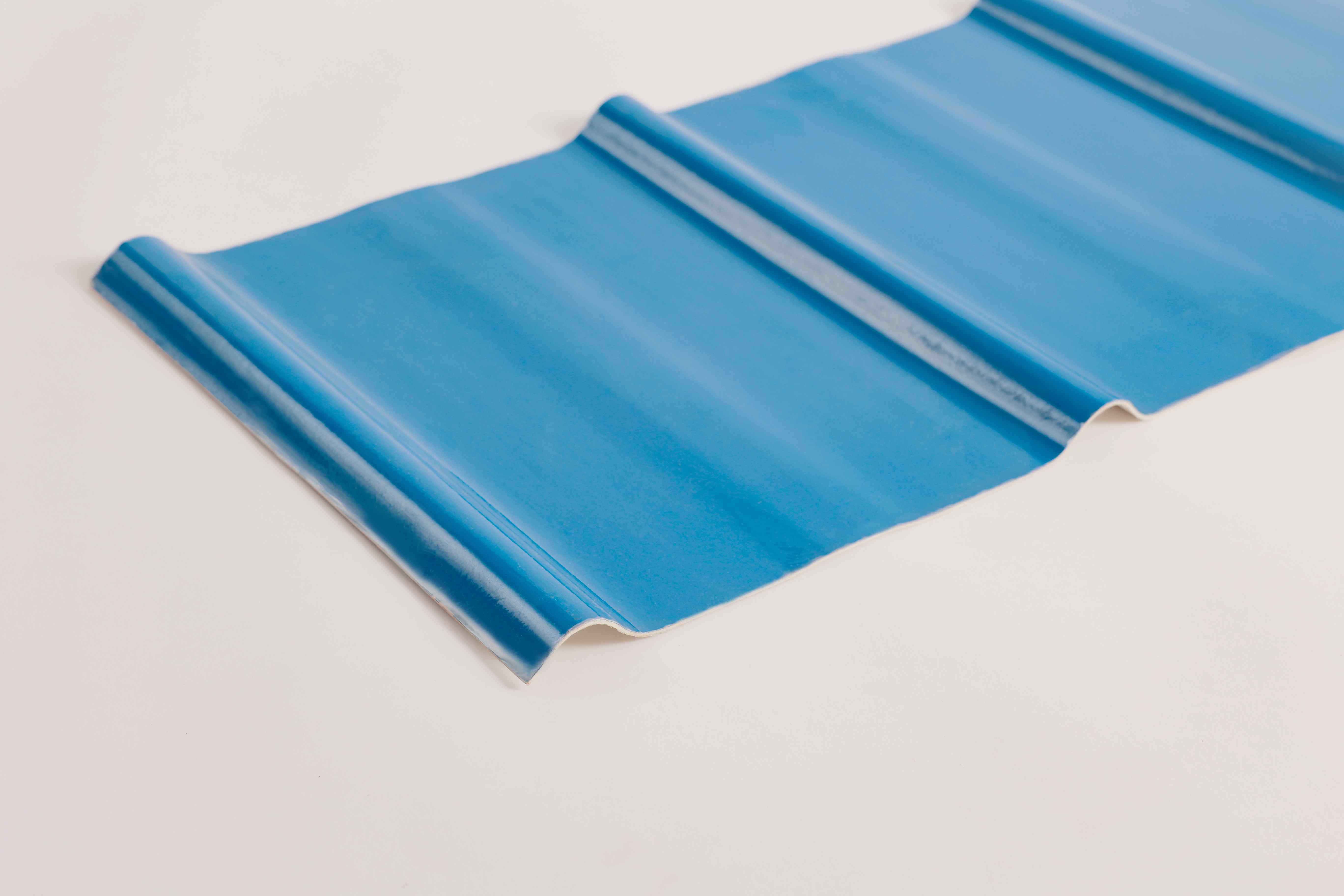
Fiber Reinforced Plastic (FRP) sheets are renowned for their durability, but much of their resilience comes from a critical component: the gel coat. This specialized layer acts as the "armor" of FRP, providing both aesthetic appeal and long-term protection. Let´s explore what makes the gel coat indispensable and how it enhances FRP performance.
What is a Gel Coat?
A gel coat is a thick, resin-based layer applied to the surface of FRP sheets during manufacturing. Unlike standard paint or coatings, it is chemically bonded to the FRP substrate (typically a polyester or epoxy resin reinforced with glass fibers). This creates a seamless, non-porous barrier that becomes an integral part of the sheet. Gel coats are formulated with additives like UV inhibitors, pigments, and fire retardants to meet specific performance needs.
Key Roles of the Gel Coat in FRP Protection
Corrosion and Chemical Resistance
UV Protection
Waterproofing
Abrasion and Impact Resistance
Hygienic Surface
Aesthetic Finish
Types of Gel Coats for FRP Sheets
Isophthalic Gel Coats: Best for general-purpose corrosion resistance.
Orthophthalic Gel Coats: Cost-effective for indoor or low-stress environments.
Vinyl Ester Gel Coats: Superior chemical resistance for harsh industrial settings.
Fire-Retardant Gel Coats: Include additives to meet fire safety standards.
Custom-Colored Gel Coats: Pre-pigmented to match design requirements.
Application Process
During the continuous lamination process of FRP sheets, the gel coat is evenly applied on the upper film by a scraper, and then cured by a heating oven. Moving with the upper film the gel coat adheres to the resin and glass fiber.
Maintenance Tips for Gel-Coated FRP
Clean regularly with mild soap and water to remove dirt or contaminants.
Avoid abrasive cleaners or tools that could scratch the surface.
Inspect periodically for cracks or chips; minor damage can often be repaired with gel coat patching kits.
The gel coat is the unsung hero of FRP sheets, combining defense against environmental and mechanical stressors with a sleek, customizable finish. By understanding its role, industries can maximize the value of FRP in demanding applications.